This high-precision shuttle unit, equipped with 16 individually adjustable vacuum suction cups, was specifically developed for the safe and efficient transportation of custom-made plastic panels in insulation technology. The distinctive shapes and often delicate surfaces of these panels require millimeter-accurate positioning of the suction cups to prevent slipping or damage during transport. The vacuum suction cups are configured to automatically adapt to the contours of the panels, ensuring optimal grip through even pressure distribution. This enables not only stable transport but also the handling of panels with complex geometries, which are frequently used in insulation technology for specific isolation tasks.
The application possibilities of this shuttle unit, however, are not limited to insulation technology. Through modular adjustments to the number of suction cups, the size of the suction surfaces, and the control software, the system can be flexibly adapted to a wide range of industries. In the food industry, for example, similar shuttle units could be used for handling hygiene-sensitive packaging, where additional attention would need to be paid to stainless steel components and easy-to-clean surfaces.
Another advantage of the vacuum lifting shuttle lies in its scalability. Depending on requirements, the units can be equipped with additional sensors to monitor parameters such as temperature or moisture in the transported materials, enabling early detection of quality fluctuations. Integration into existing automation environments is also easily achievable through standardized interfaces, allowing the shuttle to seamlessly integrate into Industry 4.0 processes. By combining high-precision control, modular design, and industry-specific adaptability, the vacuum lifting shuttle thus represents a versatile solution for complex transport tasks in modern production environments.
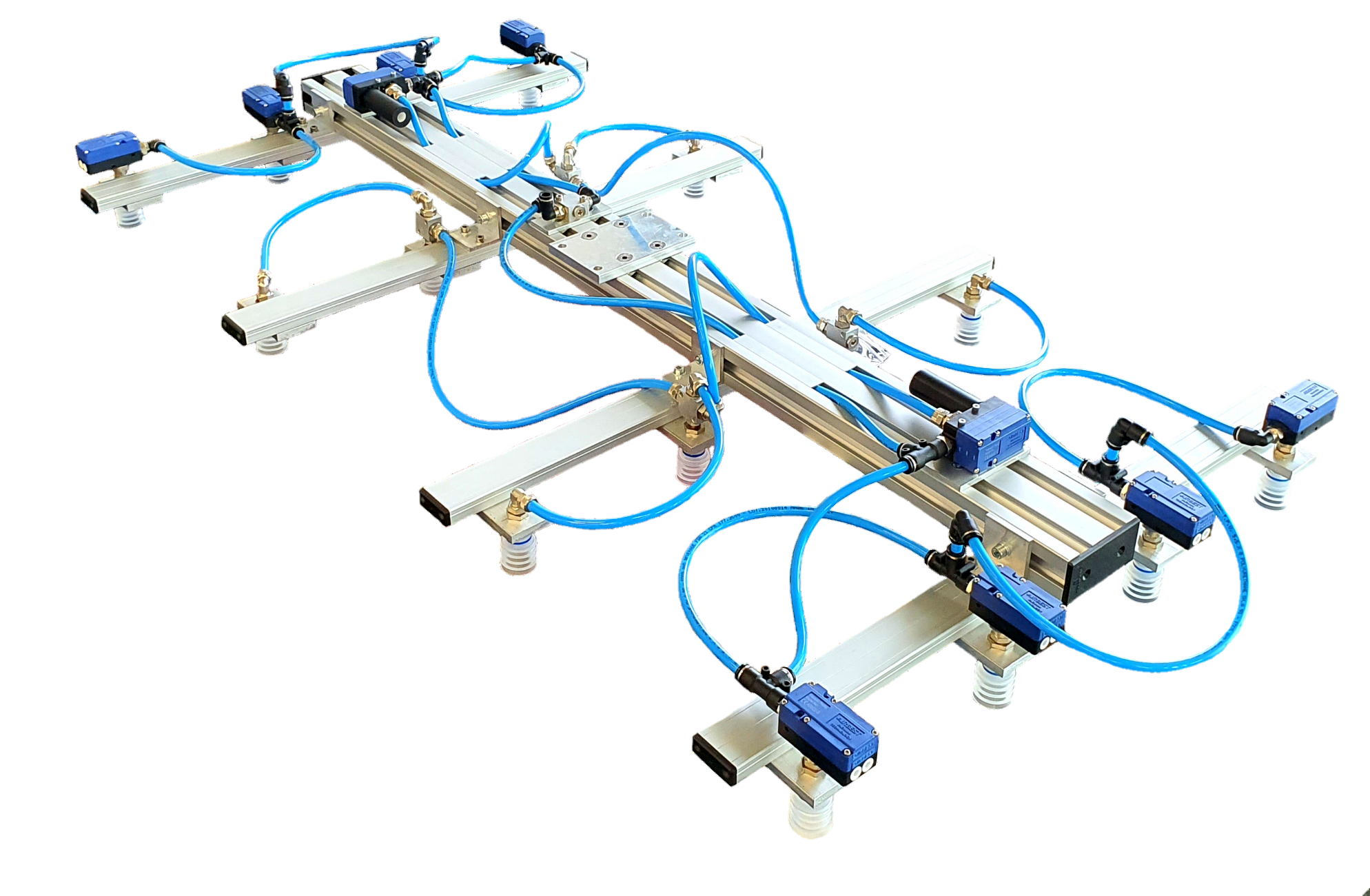
Specifications & Details